Building Products
INVEX software built for service centers focused on producing building materials
The INVEX metal software offers a comprehensive set of features and functions that are specific to companies that produce profiled panels and metal building composite panels made from pre-painted and coated metals.
Common business cases such as producing painted slit coil and roll forming the slit product into a profiled panel or flashing, can be handled quickly and out-of-the-box. Other common processes include composite panel manufacturing, cut-down front/exit shearing, press brake/folding, slitting, painting, and anodizing.
In addition to profiled panels and composite panels, these building products companies, also referred to as metal roofing service centers, handle and manufacture a variety of other products that include flashing, roof underlayment, fixtures, fittings, fasteners, and accessories.
Orders can be fulfilled using the multi-step routing function that can fulfill an order across a single or multiple warehouses.
This can include outside processing steps; all required transfers are automatically created.
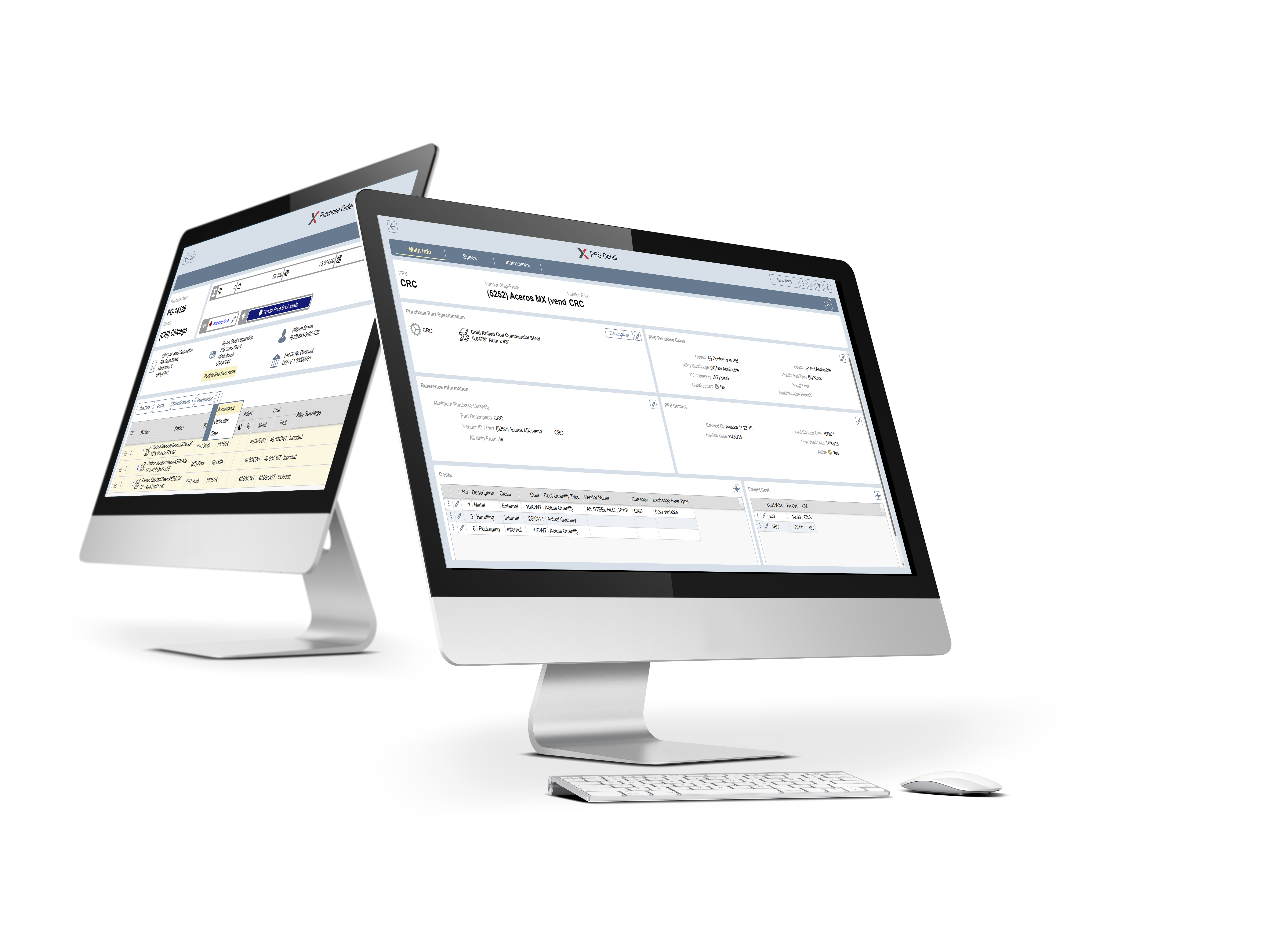
Cases Handled
PAINTED COILS
INVEX handles bare coil, coated and painted coil inventory as well as the slitting and cut-to-length processes to produce the slit coil and sheet.
PROFILED PANELS
Profiled Panels are produced by roll-forming flat metal products into profiled or grooved panels. For sales and production purposes, INVEX tracks both the consumed width of the flat metal as well as the finished width of the profiled panel.